Introduction
AAC blocks, also known as autoclaved aerated concrete blocks, are a revolutionary construction material that has taken the market by storm in recent years. They are sustainable and environmentally certified building materials that boast several notable features. AAC blocks are lightweight, load-bearing, and highly insulating construction material that is three times lighter than traditional red bricks. Additionally, AAC blocks are known for their durability, making them an ideal choice for builders and architects looking for reliable and long-lasting building materials. In this article, we will learn everything about what AAC blocks are, their history, manufacturing process, features, advantages, and disadvantages.
What are AAC blocks?
AAC (autoclaved aerated concrete) blocks are foam concrete construction materials created by using various materials such as quartz sand, gypsum, lime, Portland cement, water, and aluminum powder. After mixing and molding, the concrete is treated with heat and pressure through autoclaving, which results in its distinctive features. In the recent construction industry, AAC bricks are highly in demand compared to conventional bricks because of their load-bearing strength and superior thermal insulation properties. They are suitable for both interior and exterior structures and can be finished with various materials, such as stucco, veneer brick, or vinyl siding.
Background and History of AAC Block
AAC blocks were invented in the early 1920s by a Swedish architect named Dr. Johan Axel Eriksson along with Prof.Henrik Kreüger. The process was first patented in 1924, and its production for use in large volume started in Sweden in 1929 in the city of Yxhult, where the first registered building materials brand in the world, called Ytong, was created. A similar solid block was established in 1939 in Sweden; currently, this block has plants in more than 35 locations across the globe.
Manufacturing process of AAC Blocks
The manufacturing process of AAC blocks involves several stages.
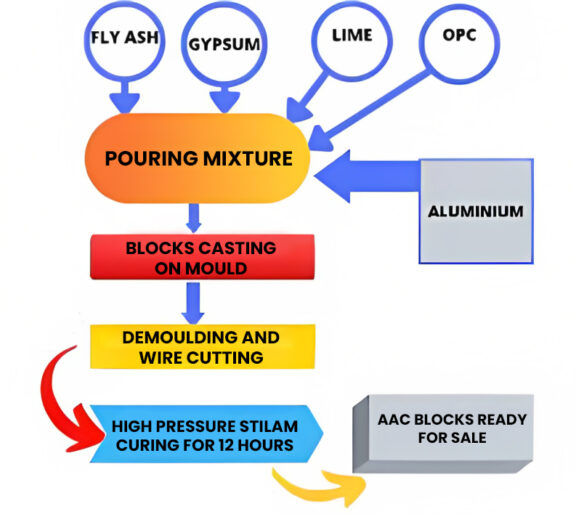
- Firstly, materials such as cement, fly ash, gypsum, and aluminum are mixed in specific proportions to form a slurry pouring mixture.
- Secondly, the slurry is then poured into molds and left to rise and pre-cure.
- After pre-curing, the blocks are demolded and cut into the desired size using cutting wire.
- The final stage of the manufacturing process involves steam curing the blocks in an autoclave under heat and pressure for approximately 12 hours to give the blocks their distinctive properties.
Features of AAC Blocks
The following are the features of AAC blocks:
- Color: Greyish-white
- Lightweight: 50% lighter than red bricks
- Fire resistance: Ranging from two to six hours, depending on the thickness
- Energy efficiency: 25% reduction in air-conditioning costs
- Thermal efficiency: Higher than clay bricks
- Water absorption: Approximately 10% of its weight
- Sound insulation: Approximately 42 dB
- Affordability: AAC blocks are nearly one-third of the cost of regular bricks
Advantages of AAC Blocks
- Lightweight: AAC blocks weigh 3 to 4 times less than bricks and 30% less than concrete, reducing the weight of the building and allowing for the construction of taller buildings.
- Thermally Insulated & Energy Efficient: The small air pores and thermal mass of AAC Blocks provide excellent thermal insulation, which reduces heating and cooling costs.
- Eco-Friendly and Sustainable: AAC Blocks are made with materials like recycled industrial waste (fly ash) and non-toxic ingredients and require less energy to manufacture, which makes them environmentally friendly and sustainable.
- Workability and Design: The workability of AAC Blocks is effortless, and they offer design flexibility. They can be easily milled, cut, grooved, nailed, and drilled to meet specific requirements.
- Fire Resistant: AAC Blocks are fire-resistant and can withstand direct exposure to heat up to 1600°C for up to 6 hours.
- Acoustic Performance: The porous nature of AAC Blocks makes them great for sound absorption, which makes them ideal for structures like hospitals, schools, hotels, and offices that require acoustic insulation.
- Seismic Resistant: AAC blocks are lighter in weight, which reduces the impact of earthquakes on buildings. Additionally, their non-combustible nature provides an advantage against fires that can occur during earthquakes.
- Faster Construction: AAC Blocks come in various sizes; as such, bigger sizes of AAC require fewer joints, ultimately resulting in reduced construction duration. The lightweight criteria of AAC blocks also make them easy to transport and construct, speeding up construction time.
Disadvantages of AAC Blocks
Although AAC blocks offer several advantages, there are also some drawbacks to using them. These include:
- Cracking: AAC blocks can develop cracks after installation if not done correctly or installed during rainy weather. To prevent this, the strength of the mortar should be reduced, and the blocks should be kept dry during and after installation.
- Handling: Due to their brittle nature, AAC blocks require careful handling to avoid breakage, especially compared to more durable clay bricks.
- Installation: AAC blocks need to be installed properly, or it can lead to structural cracks and affect the final look of the building.
- Limited load-bearing capacity: As AAC blocks are lightweight, they may not be the best choice for load-bearing walls that require significant strength.
- Installing other features: When fitting cabinets and wall hangings, longer and thinner screws should be used along with wood-suitable drill bits or hammering in. This is because of the brittle nature. Some builders prefer to use traditional building methods to install an extra layer of insulation around the entire building, as the insulation requirements in newer building codes of many countries in Europe would require building thick walls.
Top AAC Brands in India
- Siporex Block
- Magicrete
- Renacon AAC Blocks
- JK Lakshmi
- Aerocon Blocks
- Ultratech Xtralite AAC Block
- Birla Aerocon AAC Block
- Ambuja Cool Wall AAC Blocks
Conclusion
In the above paragraphs, we learned what AAC blocks are. They are a popular building material due to their many advantages, including high strength, low density, good thermal insulation, and fire resistance. The manufacturing process of AAC blocks involves mixing fly ash, cement, lime, gypsum, aluminum powder, and water to form a slurry that is poured into molds and cured under high pressure and temperature. The resulting blocks are lightweight, durable, and easy to work with, making them a popular choice for construction projects. As we discussed above, the history of AAC blocks dates back to the early 20th century, with commercial production starting in Europe in the late 1920s. Today, there are many top AAC block brands in India, including Siporex, JK Lakshmi, Biltech, Renacon, Magicrete, and Aerocon Blocks, each offering unique features and benefits. These AAC blocks can be conveniently ordered from Builders9. With the increasing demand for sustainable and eco-friendly building materials, AAC blocks are becoming a preferred choice for builders and contractors across the world.