Cement is a predominant material in the construction industry, as it acts as a major binding material in concrete making. It has been extensively used for urban development, including highways, bridges, structures, and much more. The annual production levels of cement are increasing rapidly every year. It is estimated that the cement yield will surpass 5 million tons by 2050. There is no surprise in those metrics, as cement is the 2nd most used commodity after water.
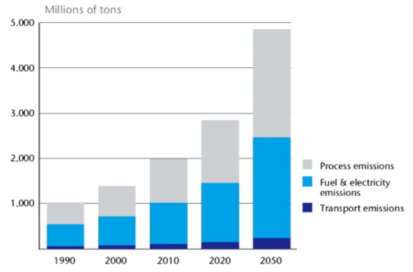
Why is the cement manufacturing process not environmentally friendly?
In the manufacturing of cement, the process includes the blend of limestone and clayey soil being subjected to 1400°C in the kiln. Followed by the thermal process, the treated material is crushed to form a thick substance named clinker. Lastly, the clinker is mixed with the gypsum, which results in cement formation.
During the production of clinker and other processes of cement production, it evolves in intense high energy and emits toxic gas effluents. It is observed that 0.6-1 ton of carbon dioxide is released for every 1 ton of cement production, which leads to a cause of industrial air pollution.
As important as cement is, the process to manufacture it is also a major cause of industrial air pollution. Clinker production, a key ingredient in cement, is a major source of toxic gases, especially carbon dioxide.
Green Cement is the Solution
Keeping in mind that cement manufacturing leads to deadly gaseous releases and CO2, cement production cannot be stopped. It is unimaginable to think of a world without cement production in this fast-moving world. Green cement can be the solution to cut down the emissions produced in the conventional manufacturing process of cement. Cement production can be altered to a pollution-free manufacturing process.
What is green cement?
Green cement is the cement that helps fix the serious industrial pollution issue in a sustainable way of living. Thus, the process involved in this is the carbon-negative manufacturing process. Here in this process, the technology is used in such a way that it brings down the emissions during various operations. Thus, the resulting final product is referred to as green cement. Due to the fact that it minimizes the carbon emissions in cement manufacturing and helps to resolve serious environmental issues, it is termed green cement.
Types of Green Cement
Based on several advanced technological attempts, various types of green cement were produced. The technological advancements include carbon-negative cement, reduced carbon production practices, geopolymers, and modern concrete products. Green Cement reduces cement consumption and utilizes industrial wastes such as fly ash and blast furnace slag as primary raw materials.
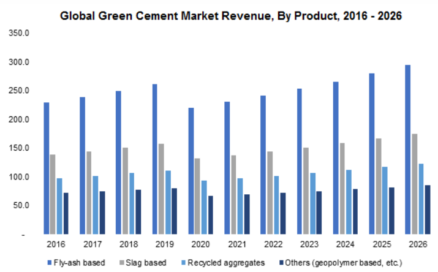
There are 6 major types of green cement. They are as follows:
1. Geopolymer Cement:
It is manufactured from aluminosilicates, which can be obtained from fly ash. Hence, it is named alkali-activated cement. It emits 95% less carbon dioxide (CO₂) than ordinary Portland cement (OPC). In terms of cost & performance, geopolymer cement is identical to ordinary Portland cement.
2. Calcium Sulfoaluminate Cement:
Calcium sulfoaluminate cement reduces energy consumption as it requires less temperature when compared to conventional cement. This results in a reduction of 25% of energy consumption, which leads to 20% lower carbon emissions. This cement setting time is so rapid that it can reach the strength of 28 days of conventional concrete in just 24 hours. So, this type of cement can be abundantly used for bridge decks and airport runway construction.
3. Magnesium Oxychloride Cement:
This cement is manufactured from magnesium mining byproducts, namely magnesium oxide (MgO) powder and a concentrated solution of magnesium chloride (MgCl₂). This type of cement is eco-friendly and carbon-neutral cement with high compressive strength and a quick setting time. But water can reduce the strength of MOC, and that can be managed to some extent by using additives such as fly ash. These additives help improve the resistance of MOC. But this cement is not recommended for reinforced concrete works, as it leads to steel corrosion.
4. Sequestrated Carbon Cement:
This was produced by The Calera Corp., a cement company in California. This cement is manufactured using seawater and brine compounded with CO₂. In the manufacturing process, the gases that consist of CO₂ can be filtered through seawater. This cement can be an alternative to Portland cement.
5. Ekkomaxx Cement:
The United States-based Ceratech Company developed Ekkomaxx Cement. It comprises 95% fly ash and 5% renewable liquid additives. The United States Green Building Council and International Code Council standards for this cement have nearly zero carbon footprint. Ekkomaxx cement has high crack resistance, high strength, resilience, sulfate attack resistance, and corrosion resistance.
6. Ferroconcrete:
This cement was invented by scientists at the University of Arizona. It is produced by the byproducts of the steel and glass industry, namely silica and iron. The mixture of those materials is then cured in the presence of carbon dioxide (CO₂), and consequently, a carbon-negative cement material is formed.
Benefits of Green Cement
Low Carbon Emissions:
Green cement is manufactured using advanced techniques that reduce the carbon dioxide emissions by 80%. Thus, resulting in considerably less air pollution
Energy Conserving:
Lowering the carbon emissions minimizes the heat energy required in the manufacturing process. Thus, the non-renewable resources can be reduced
Industrial Waste Utilization:
In manufacturing certain types of green cement, industrial waste or byproducts such as fly ash, blast furnace slag, silica, and iron are used as raw materials. This helps in being economical and saving the Earth from such waste disposal
Extended Life Expectancy:
When compared to conventional cement, green cement has high fire resistance & a great setting time. Thus, making the constructions made of green cement have a longer life span.
Choose Green Cement for a Sustainable Way of Living that a World Needs Today