Get the complete guide on molding sand properties and its types. Molding sand, also known as foundry sand, is a type of sand that is widely used to create molds. Although high-quality silica sand is mined, natural sand found on the beds and banks of rivers provides a greater source. Chemically, the sand is SiO₂, silicon dioxide in granular form. Aside from silica grains, ordinary river sand contains a percentage of clay, moisture, non-metallic contaminants, and traces of magnesium and calcium salts. This sand is used to build a mold once it has been properly treated.
1. Porosity:
The most significant attribute of molding sand is porosity, also known as permeability. It refers to the molding sand’s capacity to enable gases to move through. During the pouring of molten metal into the sand hole, gases and steam are produced.
2. Cohesiveness:
Sand’s cohesiveness refers to its ability to hold its particles together. It can be characterized as the molding sand’s strength. This feature is critical for the mold’s delicate shapes to be preserved.
3. Adhesiveness:
Sand has the property of adhesion, which causes the sand particles to adhere to the sides of the molding box. The sand’s adhesiveness allows the cope to be lifted properly with the sand.
4. Plasticity:
Plasticity is a feature of molding sand that allows it to flow to all corners of the mold when rammed, eliminating the possibility of left-out gaps and allowing it to take on a specified shape under ramming pressure.
5. Flowability:
The ability of molding sand to freely flow and fill recesses and fine details in the pattern is referred to as flowability. It varies depending on the moisture content.
6. Collapsibility:
The property of sand that causes the sand mold to collapse automatically once the casting has solidified is called collapsibility. After the casting is withdrawn from the mold, it should disintegrate into small particles of molding sand with minimal force.
Sand is a granular mixture of small rock grains and granular elements that is primarily defined by size, being finer than gravel but coarser than silt. And they come in sizes ranging from 0.06 mm to 2 mm. Silt is defined as particles larger than 0.0078125 mm but smaller than 0.0625 mm.
Different Sands and Their Properties:
1. M Sand:
The manufactured sand has a critical fine gradation, physical features including shape, even external touches, and consistency, making it the best sand for building. With reduced separation, honeycombing, bleeding, voids, and capillary action, concrete is infused with great strength from sand’s physical qualities.
Accordingly, the estimated grade of sand helps the concrete fill voids between coarse aggregates and makes the concrete more compact and dense, enhancing the strength of the concrete.
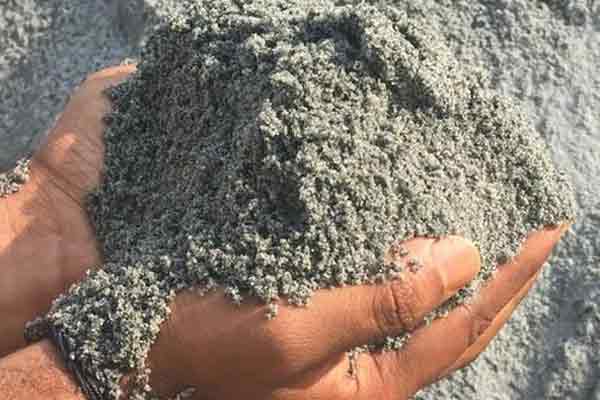
2. Green Sand:
Flexible production, high productivity, short production cycles, and ease of organizing continuous production and implementing mechanization and automation production processes; materials are inexpensive.
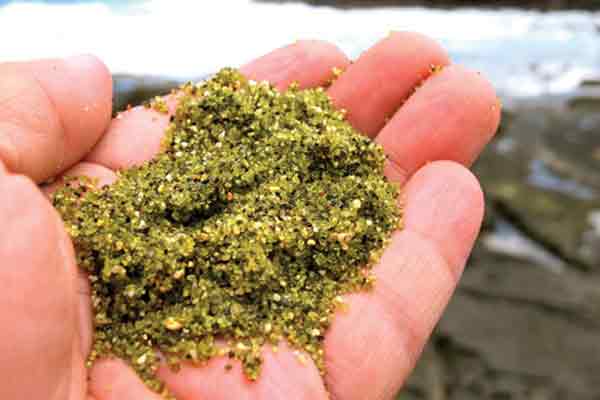
3. Foundry Sand:
The most significant attribute of molding sand is porosity, also known as permeability. Sand’s cohesiveness refers to the ability of the sand to hold its particles together.
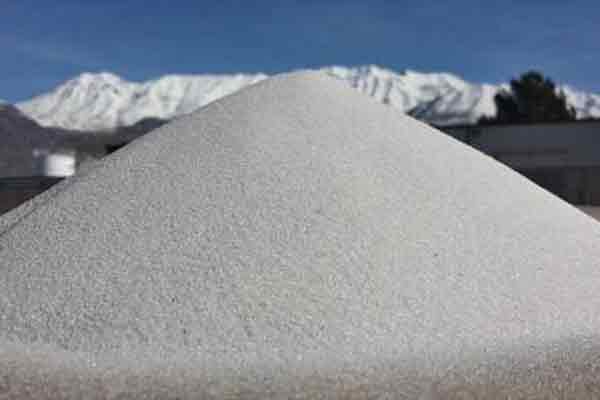
4. Silica Sand:
Under normal temperature and pressure, silica is a solid, crystalline mineral that is relatively hard. Pure silica is colorless; however, if impurities are present in a quartz sample, it may be tinted. Silica has extremely high melting and boiling temperatures of 3,110°F and 4,046°F, respectively.
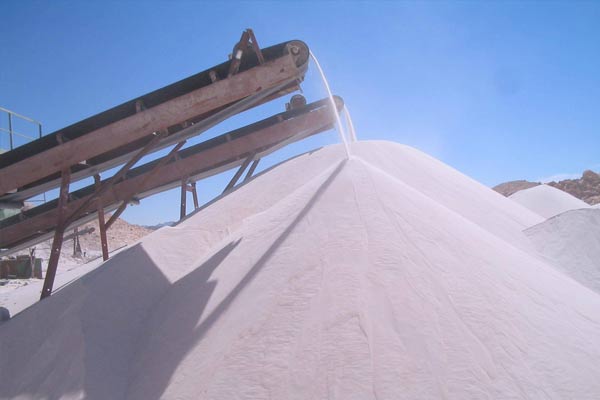
5. River Sand:
For all curing ages, river sand concrete had higher density and compressive strength than quarry dust concrete. River sand concrete had a 36 percent higher compressive strength than quarry dust concrete after 28 days of curing, whereas quarry dust concrete had a 12 percent lower compressive strength.
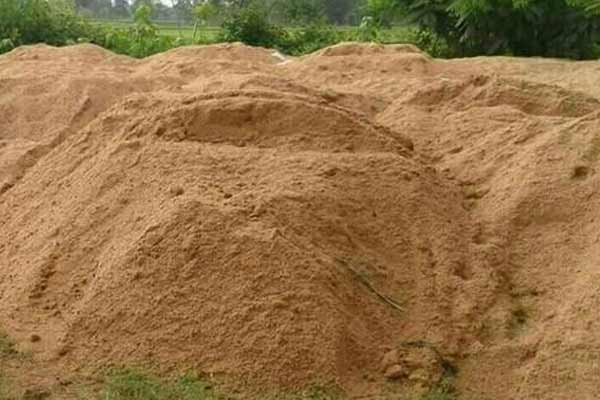
Check it out: 8 Salient Things You Need To Know While Selecting Tiles For Your Dream Place